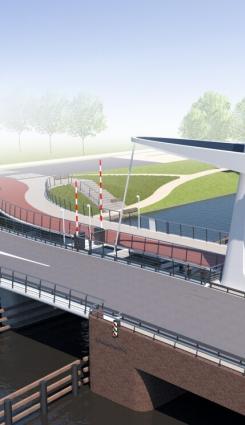
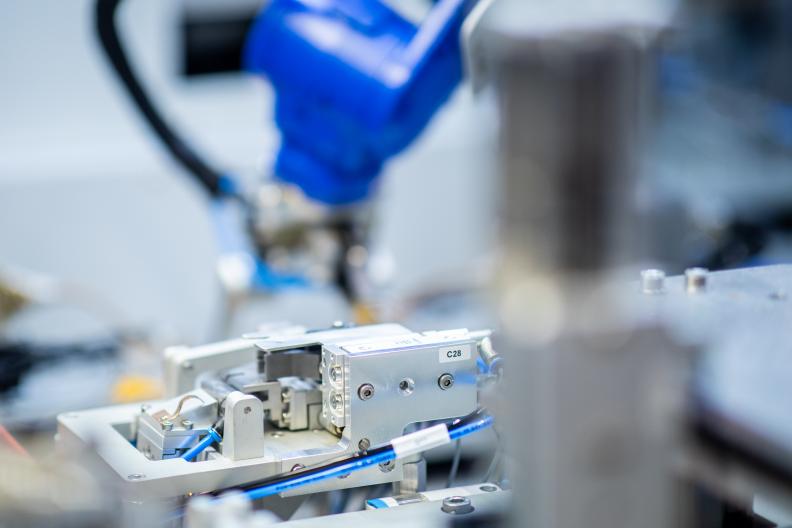
Kennisplatform
High Precision Assembly
Customer - KROHNE Altometer Dordrecht
In the development from manual production to full automation the customer asked us to develop an assembly and validation solution for the production of industrial flow meters.
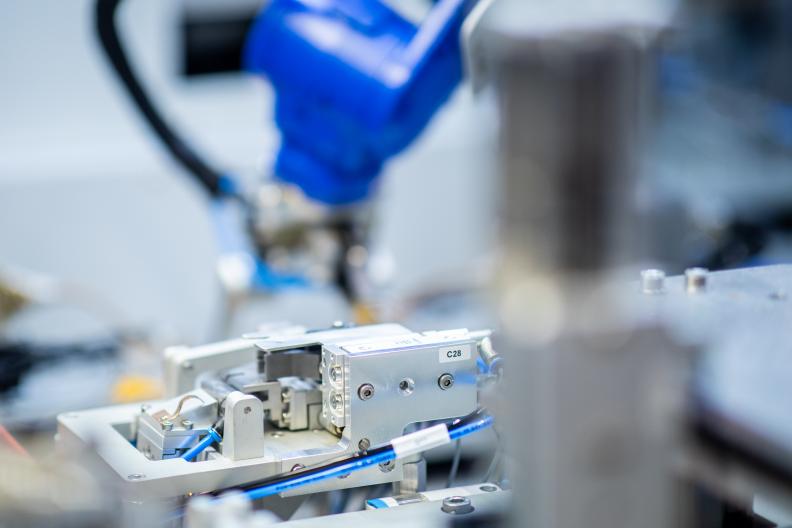
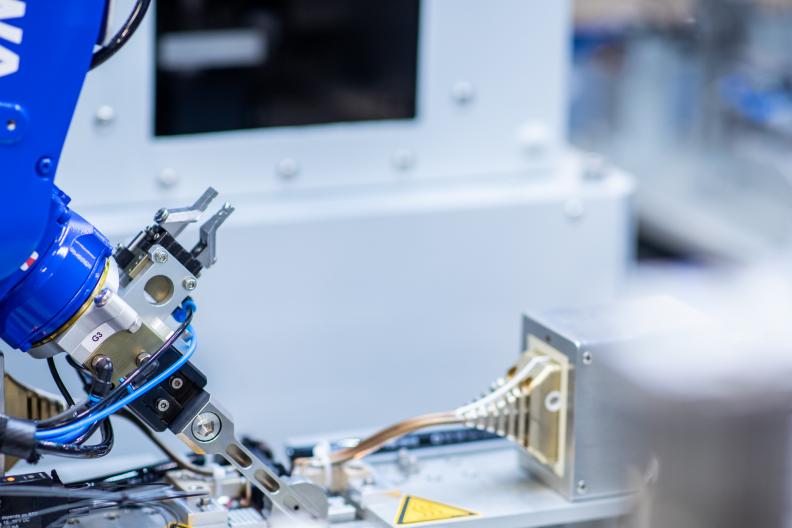
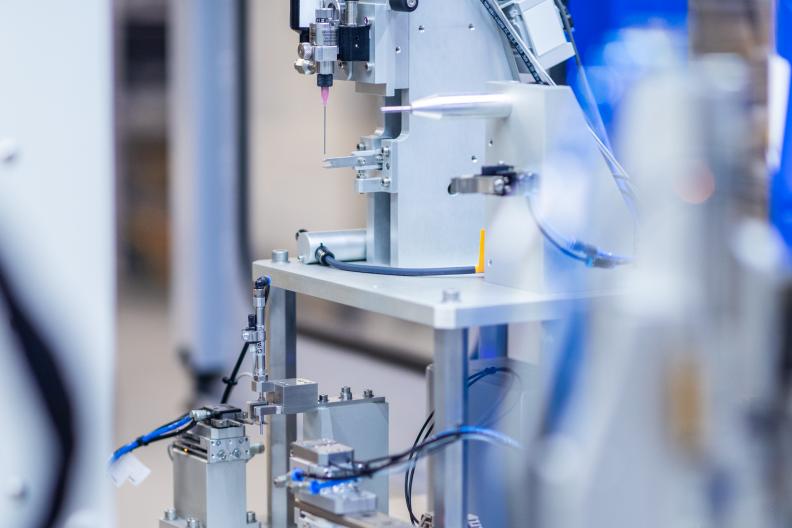
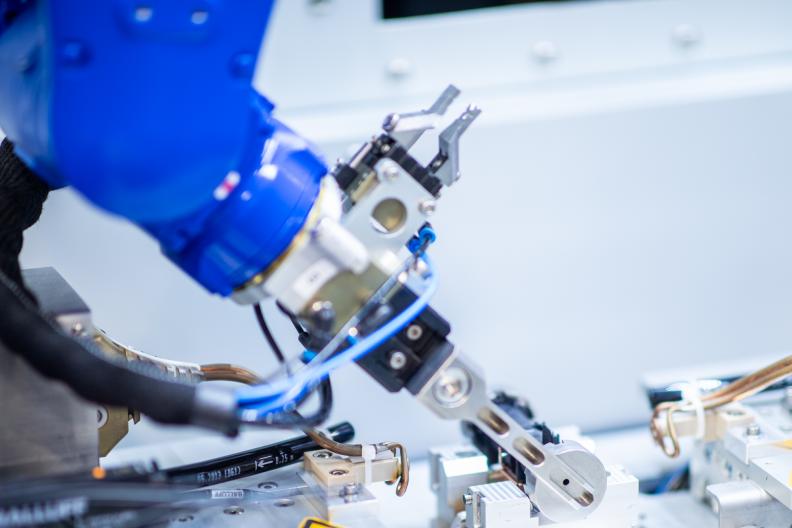
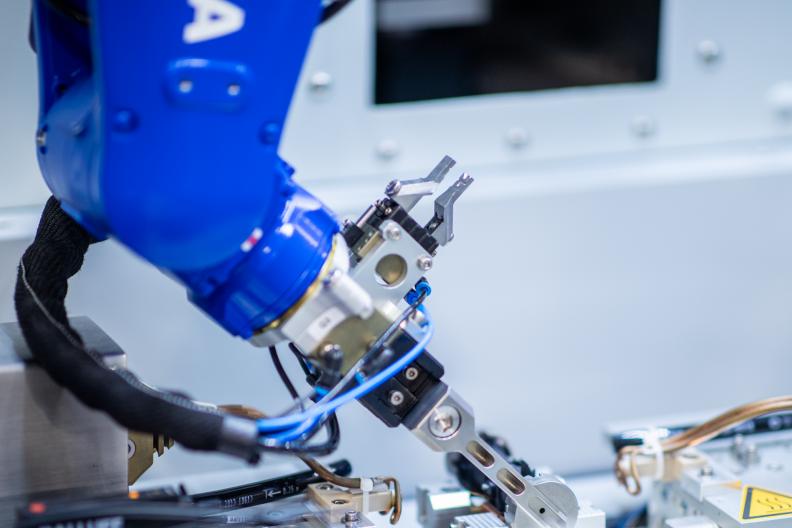
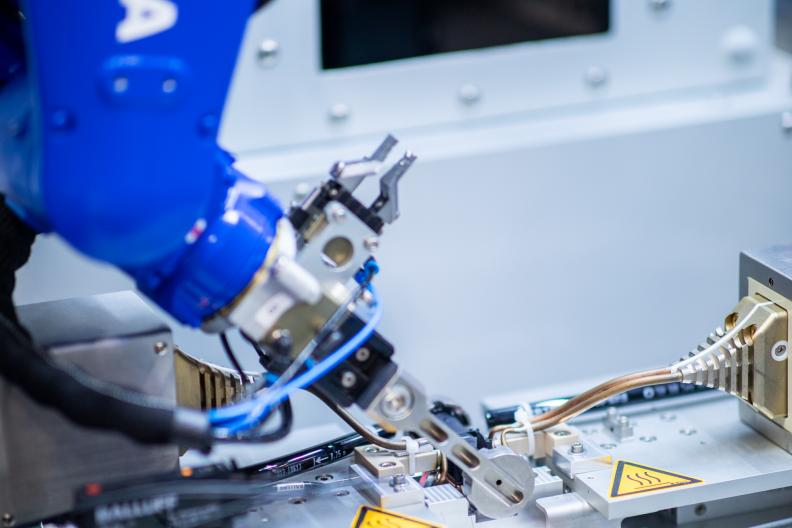
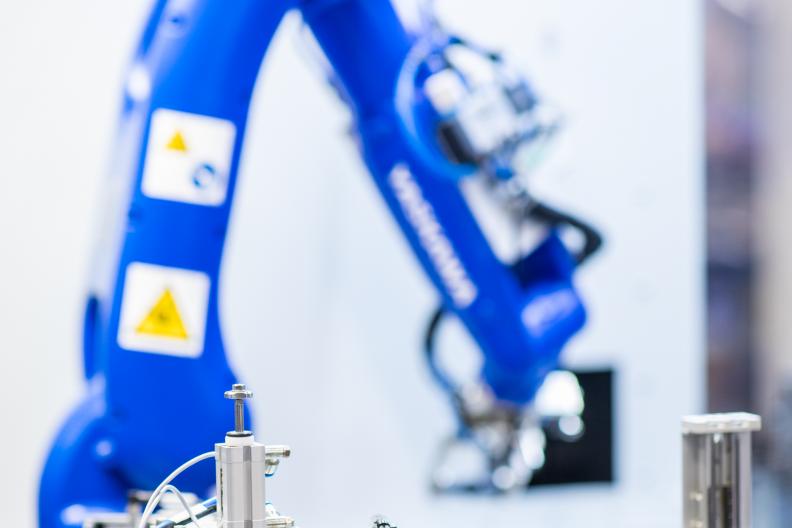
The customer produces various kinds of process instruments. For the realisation of a new type of flow meter they wanted to step towards a fully automated solution. One of the challenges in this process was the very restricted floor space in combination with high amount of varying process steps and a variety of product ranges to be produced.
Our competence expertise
- Product traceability
- Soldering
- Gluing
- Laser welding
- Product assembly
- Full automatic test station for measuring pressure, flow, temp and impedance
Our solution
We designed and realised a fully automated assembly station for the assembly of the customers’ new product. During this process we helped the customer on design for automated assembly of its product. The finished cell contains a large set on varying assembly steps. Some steps are: soldering, pressing, laser welding, bending and gluing. Each finished product will be tested in an integrated end of line inspection station in which electrical connections and several other parameters will be checked at high pressure. 4 different product types can be produced in this system.
Product supplied to and from the machine can be done by operators without affecting the machine flow using drawers within a safety enclosure. During the assembly process all process data is stored ensuring full product traceability.
Other competences used in this solution:
- Robotic Handling (including non-precise parts and flexible electro cables)
- High Precision assembly
- Vision